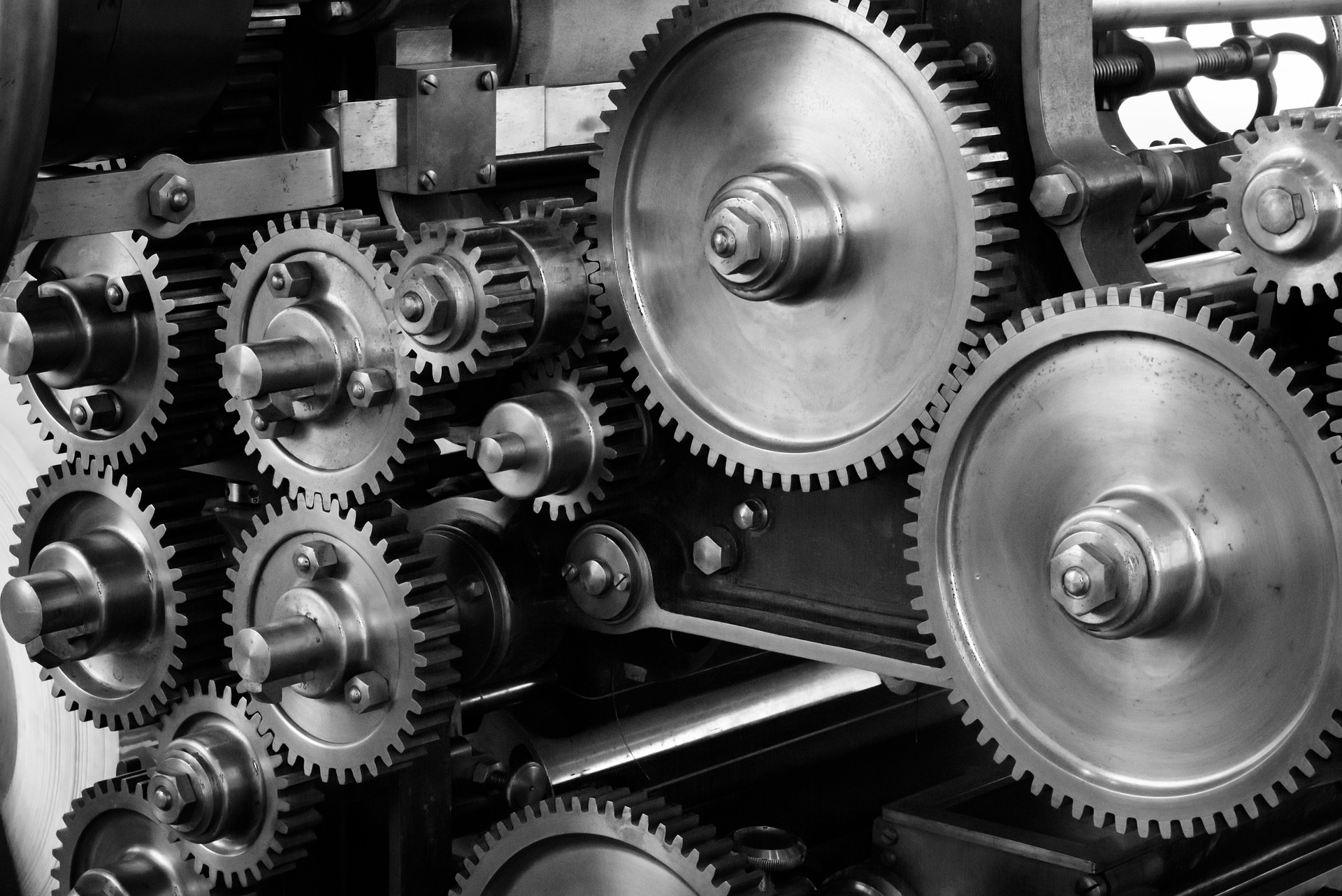
Lubrication pumps are a vital component of large industrial machinery applications. Lubrication pumps are used in the process of conveying different types of lubrication to the areas it is needed to protect industrial equipment from wear and tear, while also maximizing the efficiency and reducing production costs.
In today’s article, we will discuss two different types of lubrication pumps and some of their most common applications, along with some important information on how to increase their usefulness.
Types of Lubrication Pumps and How They Work
There are two basic groups of lubrication pumps: oil pumps and grease pumps. Although both types of lubrication pumps are commonly used in running industrial machinery, they serve different functions in the production process. However, they do share some similarities in terms of maximizing their efficiency.
Grease Pumps
Grease pumps are a class of lubrication pumps that are used for lubricating the inner components of large industrial machinery, and they generally have a few common characteristics that will be consistent across most models.
Grease pumps can range in size and strength depending on their application, but they are made up of four common components that will be found on nearly every model of this lubrication pump device.
Reservoir - Grease pumps have a grease housing reservoir that is usually made out of clear plastic so you can accurately measure the amount of grease when filling the machine and continue to check the level of remaining grease. Maintaining the integrity of the lubrication pump reservoir is important because it protects the grease from becoming contaminated with dust, dirt, and moisture.
Pump mechanism - The pump mechanism is the lubrication pump component responsible for moving the grease from the reservoir to the lubrication points. It accomplishes this by creating pressure within the reservoir to force the grease out of the reservoir and into the grease lines. The pump mechanism will generally use either an electric motor or air to create the necessary pressure.
Pump controller - The pump controller is a metering device that measures the amount of grease being transferred into the lubrication lines. The pump controller can use a pressure valve to accomplish this, but in most industrial applications, it will employ an electronic feedback system to accurately measure the amount of grease needed at the lubrication points.
When setting up your grease lubrication pump, you will need to configure your pump controller according to the type of grease you are using and the specific lubrication needs of the machinery.
Lubrication lines - Lubrication lines are small hoses made from synthetic materials that transport the grease from the lubrication pump to the lubrication points of the machinery. When attaching the lubrication lines to your lubrication pump, measure out the necessary distance from the pump to the lubrication point and cut the hose to the appropriate length. The lubrication line can then be attached to the lubrication pump outlet and fed to the lubrication point.
Grease lubrication is a type of lubrication that contains either natural or synthetic oil and is combined with a thickening agent that is akin to soap. Because it has a higher viscosity than other types of lubrication, grease has a greater ability to stay in place and provide longer-lasting lubrication.
Oil Pumps
Oil pumps are a type of lubrication pump that is used across a wide variety of applications within industrial machinery. Oil pumps can be used to provide lubrication to gears moving parts, create pressure for hydraulics systems, and deliver a continuous supply of oil that acts as a coolant for grinding and cutting.
While oil pumps can differ in their overall characteristics, they contain a core set of components that are used to make this type of lubrication pump function properly.
Housing - The housing of the oil pump is its outer casing that protects the inner workings from contaminants and provides the structure to keep everything in place. Oil pump housings are typically made from steel, metal alloys, and durable forms of industrial-grade plastics.
Inlet and outlet ports - Inlet ports are the opening through which oil is allowed into the lubrication pump from an oil reservoir. Inlet ports employ a mechanism to create a controlled flow of oil into the lubrication pump system.
Outlet ports allow the flow of oil out of the oil pump and into the system where the oil is needed.
Drive shaft - The oil pump drive shaft is a rotating arm that turns the oil pump rotor. This mechanism creates the necessary pressure to provide a continuous flow of oil through the oil lubrication pump.
Rotor - The oil pump rotor is a rotating mechanism that is made up of two parts: the inner rotor and outer rotor.
The inner rotor resembles a gear, and it is housed inside of the outer rotor, which is a metal disc with a gear-shaped opening. The inner rotor has one less tooth than the outer rotor’s opening. As the inner rotor is turned by the drive shaft, it rotates within the outer rotor’s opening, and because it has one less tooth than the outer rotor’s opening, it leaves an open space that moves with every progression of the turn.
This may be hard to visualize, but you can probably picture the children’s toy that is used to create geometric shapes by inserting a pencil into a plastic gear and spinning it inside of another plastic circle. The oil pump rotor operates with a similar concept.
The opening left between the inner and outer rotor provides a space that the oil can be drawn through, and the rotational force creates the necessary pressure for the oil to be pulled in and pushed out simultaneously.
Maintaining Your Lubricant
Although these two types of lubrication pumps operate differently and have different purposes, they share one common trait across all models and variations: they can only do their jobs efficiently with proper lubrication.
Keeping your lubrication clean and free of contaminants is absolutely essential for ensuring the proper functioning of your lubrication pump system.
Here are a few best practices for maintaining your lubrication:
- Use the right type of lubricant and do not cross contaminate by combining different types of lubricants.
- Store your lubricant in a clean container and never put fresh lubricant inside a container that is contaminated with used lubricants.
- When adding lubricants to your lubrication pumps or lubrication systems, make sure that the outlet of your lubricant container and inlet of your lubrication system are free of dust and other contaminants.
- Take samples of your oil and test it for contaminants.
- Depending on the application of your lubrication pump, consider adding a filter to remove any unwanted substances from your lubrication. When using a filter, make sure that the filter size you are using is correct. If a filter is too fine, you may end up removing the additive packages of your lubricant, and if the filter is too coarse, you won’t filter anything at all.
IndustryNest Lubrication Pumps
IndustryNest offers a wide range of lubrication pumps and lubrication pump parts from one of the leading manufacturers of industrial machinery. If you are in the market for a new lubrication pump or are looking for more information about industrial machine parts, contact IndustryNest today!
Not sure what you are looking for? Check out our community of engineers to get answers for your questions from real experts!